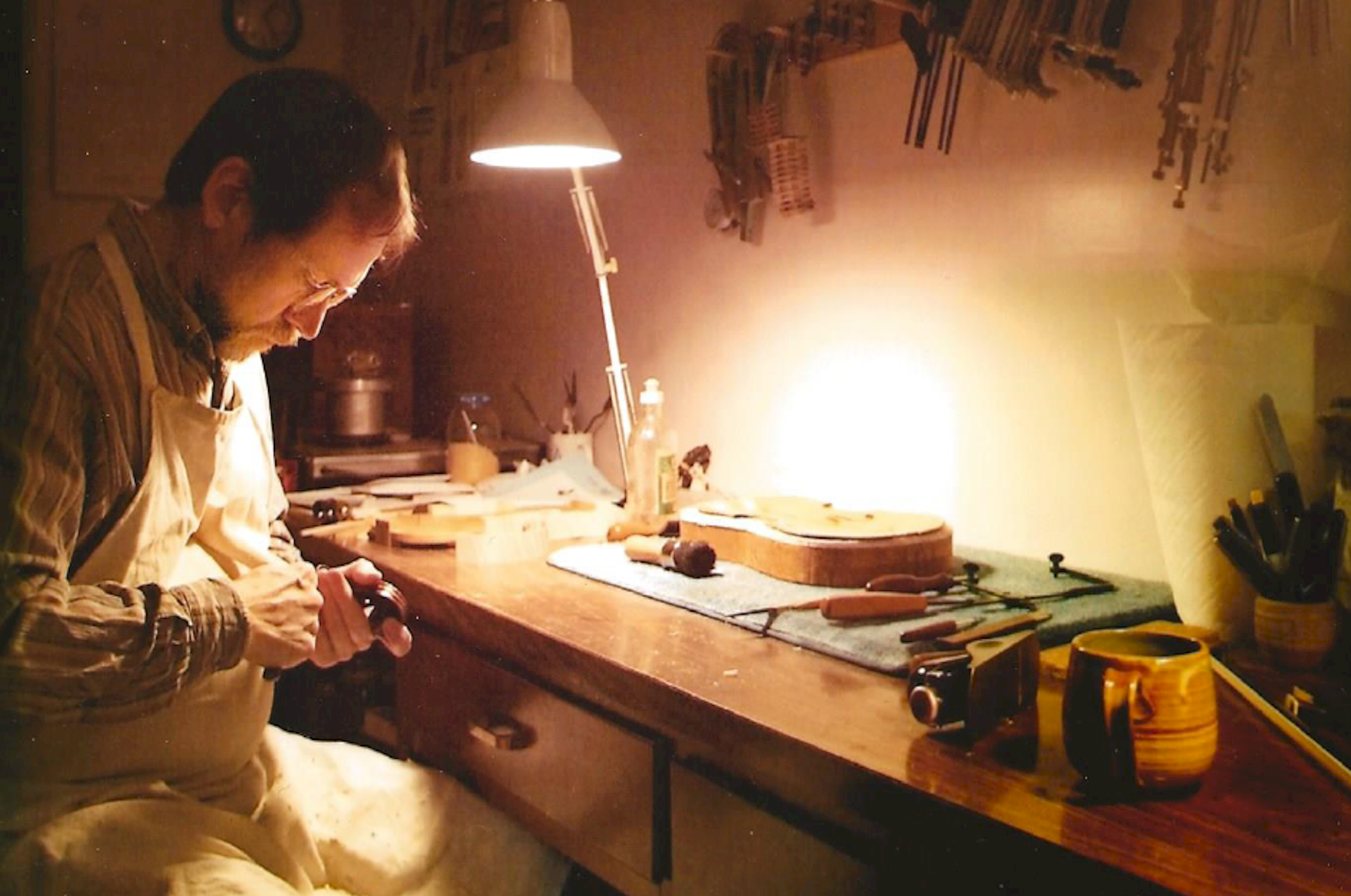
Our Approach
Thomas Verdot
After a number of years of digging for information on violin making and repair work and grasping in the dark on my own, I discovered the possibility of actually going to violin making school. I received a good, solid background in construction from the late Karl Roy, former head of the violin making school in Mittenwald, West Germany. Karl was a patient but demanding teacher. I studied restoration with Hans J. Nebel, a fourth generation “Fiddle Maker” also from Mittenwald. Hans was the former head of the restoration department of the Rembert Wurlitzer firm in New York City, NY.
I am grateful to both of these men for what they have given me. The most important lesson is always how to think and approach each project with a cautious but open mind. Every bit of damage has its own unique issues and needed solutions. Each new violin offers opportunities in style and sound.
Our Story
As a maker I have taken an interest in styles and methods from many regions but have returned to the source of most great instruments – Cremona, Italy. The construction methods of North Italian and South German makers follow the same tradition using an inside mold for forming the rib structure which dictates the overall outline of a violin. It is a very flexible method which leaves a great deal of room for individual workmanship. While it is doubtful that anyone knows specifically who used the first inside mold for making a violin, most of the earliest instruments created in this manner are from the hand of Andrea Amati in Cremona in the late 16th century.
I feel the greatest affinity for the Amati family instruments and most often work close to that visual esthetic. The end product is almost never an attempt to make an exact copy. While it is a fun sport, I seldom “antique” the finish. A Verdot violin will, like almost all makers’ instruments, be recognized by a good eye for what it is and can stand on its own merits.